A Downtuned Acoustic Ovation Project
Obviously it’s a natural progression, both from the perspective of adhering to “sh!t in equals sh!t out” and the House of Pines mission to always improve the sound of our instruments, that Leigh should embark on a project to downtune an acoustic Ovation.
He’s said before, Ovations are fantastic for downtuning because of the way the bridge is built – the strings go through the bridge parallel to the topsheet, whereas most acoustics have a pin-style bridge where the string ball ends are held to the underside of the topsheet with pins. The bridge itself is screwed to the topsheet with a bolt because of the added stress in the Ovation bridge configuration.
Here, we are starting with an Ovation TX Mod. in 25.5 inch scale length to downtune to drop A#.
If you’re going to downtune, you might as well do it in style
Leigh’s favorite Ovation is the TX D-scale, an acoustic baritone guitar made in Korea. In fact, he had one of those guitars tuned to Drop A# for years, but in his quest to be the most downtuned band in existence, that guitar would be repurposed for a Drop C0 project. In this case, a standard scale length was selected. It would be difficult, but would be good proof that downtuning a standard scale length guitar is very possible.
Knowing that Ovation guitars present some unique physical challenges to having a proper setup, namely that the saddle and pickup configuration is more difficult to customize than on a pin-style guitar bridge, a procedure for the construction of the necessary parts would need to be developed to complete a setup.
The additional strain on the guitar topsheet (although Ovation bodies are composite, the topsheet is still wood), belly can develop on the topsheet over time with very heavy string gauges and high string tension. Leigh attempted to reinforce the topsheet of the guitar with aluminum, which was an approximately 9″ long piece of square tube cut to follow an existing wood brace. This was secured with West system epoxy and was possible because there was hardly any belly on the guitar prior to downtuning, allowing for a true gluing surface.
Other guitars that have already developed a belly may need something like a Bridge Doctor to fix, which Leigh had already installed on his four other Ovations.
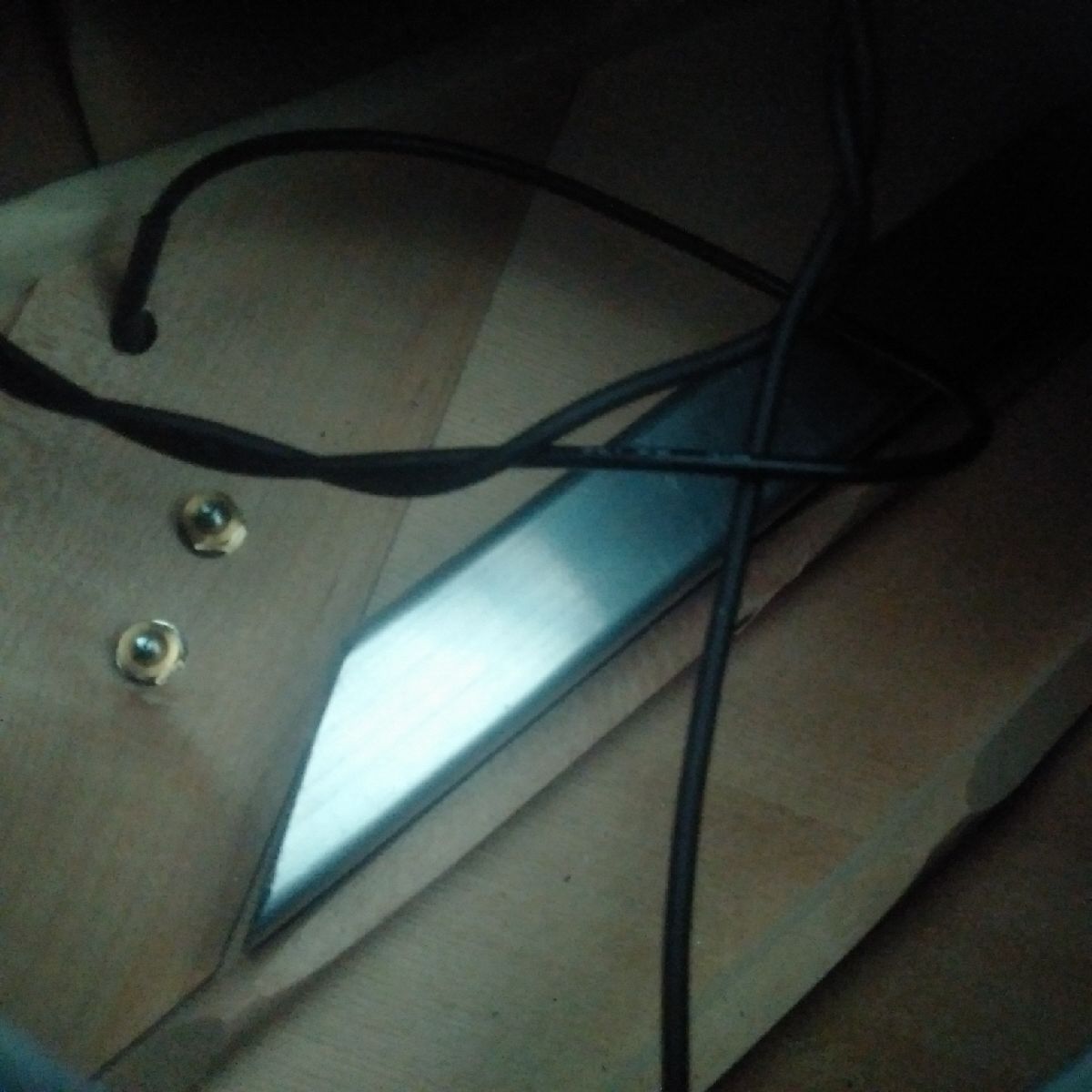
Using a string gauge tension calculator online, gauges of 17-26-32-44-60-90 were selected. Note that electric guitar strings are used. Leigh finds that electric guitar strings sound better than most people think they should on an acoustic, and they also tarnish and degrade much more slowly than bronze acoustic strings. Black and silver matches the House of Pines color scheme better anyway.
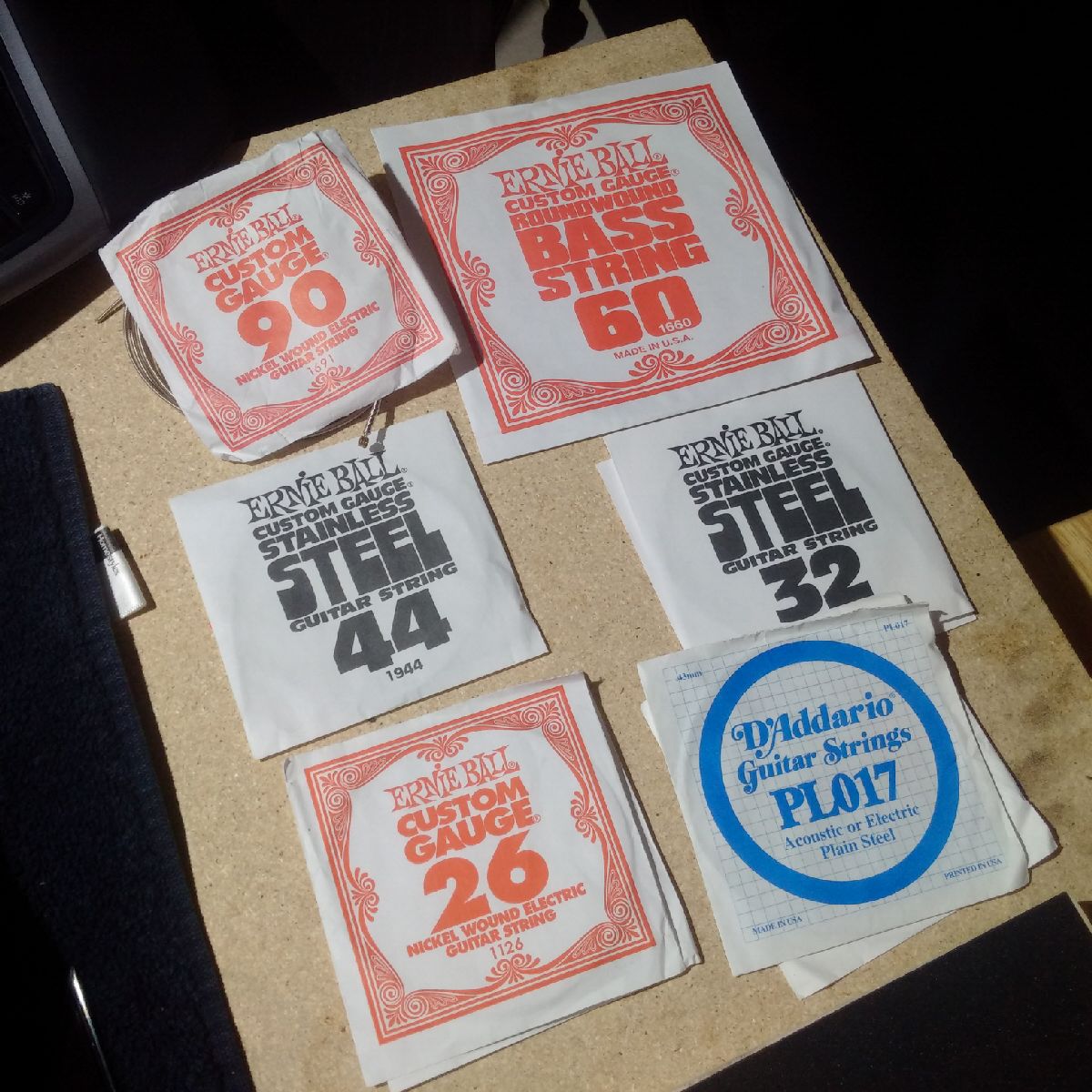
At first the goal was to install the Buzz Feiten tuning system retrofit to the guitar, however there were some expected problems with the installation. The three high-pitch strings accepted Buzz Feiten, however the bottom 3 strings needed special adjustment.
In any case, he did start by making his own Buzz Feiten shelf nut out of a GraphTech pre-slotted nut. Allegedly graphite has good acoustic properties, and the dust smells like burning tires, so bonus!
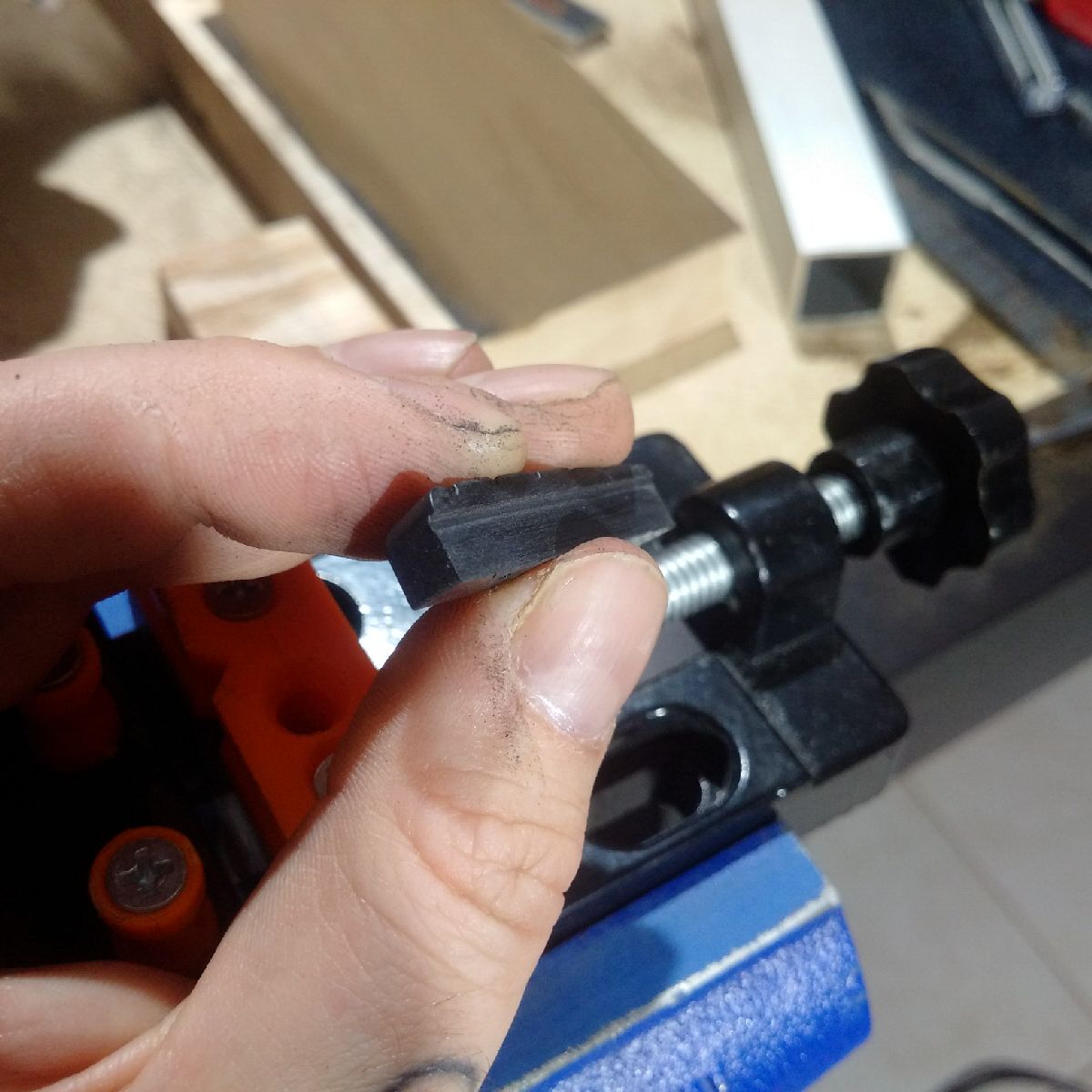
The guitar’s glorious acoustic strings were removed and kept for other projects. In order to allow the Intonator to be used, unique “flat saddles” had to be made to fit inside the Ovation pickup slot so that the brass break points would slide properly on the Ovation bridge. Don’t be fooled, these pieces took many, many hours to fabricate by hand and was the most painstaking part of the whole project.
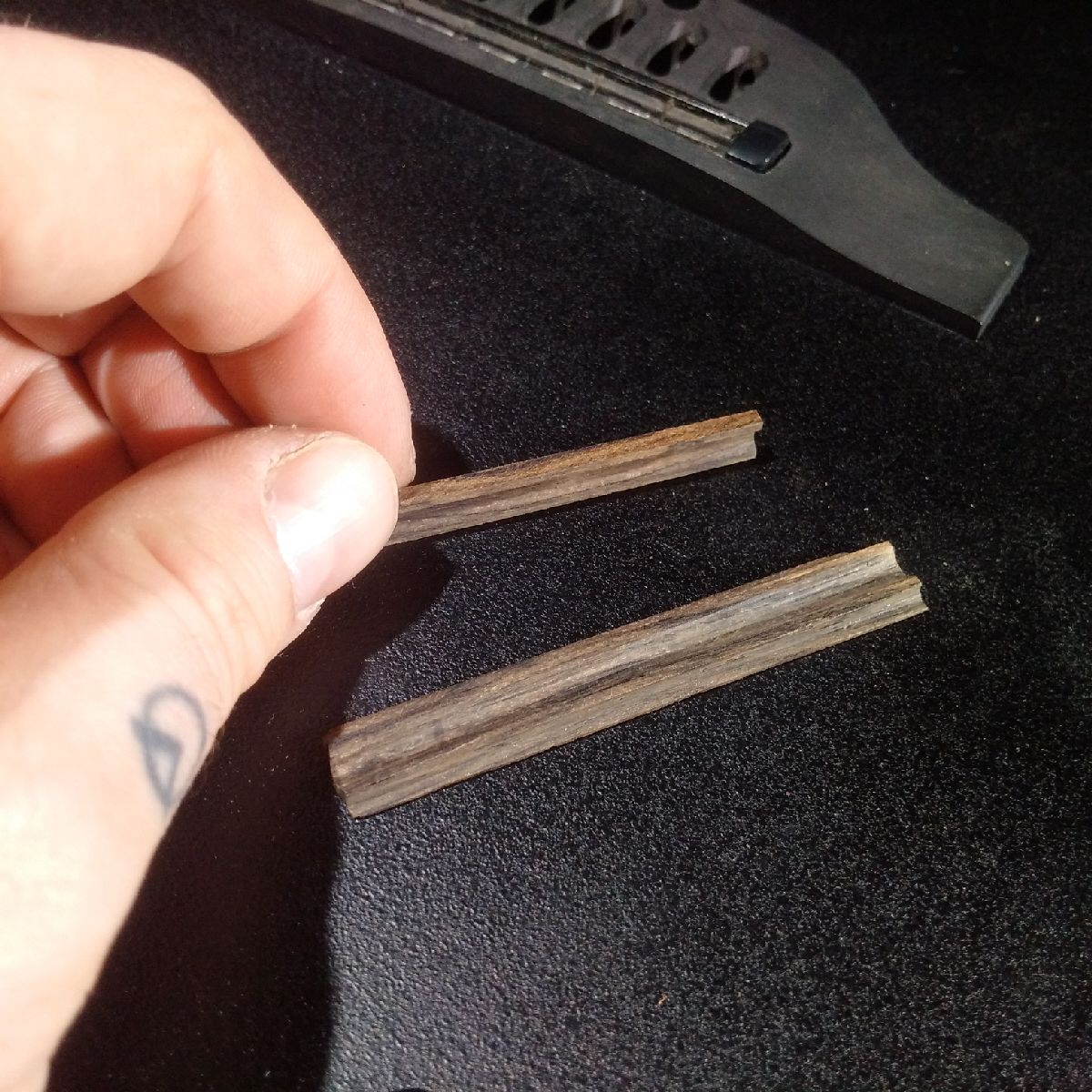
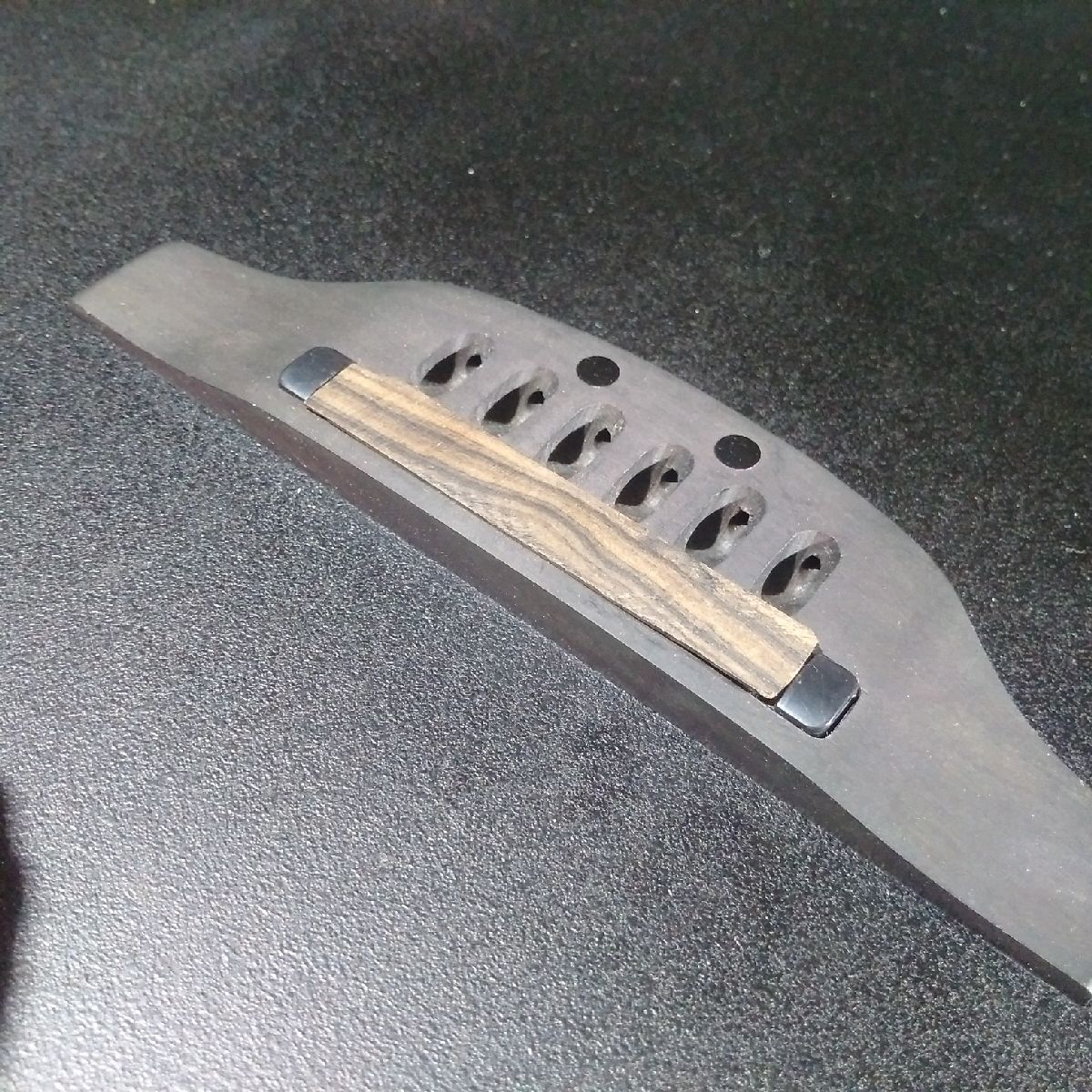
The shelf nut was shimmed and affixed, and an initial string-up was completed using the jig that was built to adapt the Intonator to the bridge (see previous blog entry for that jig’s invention).
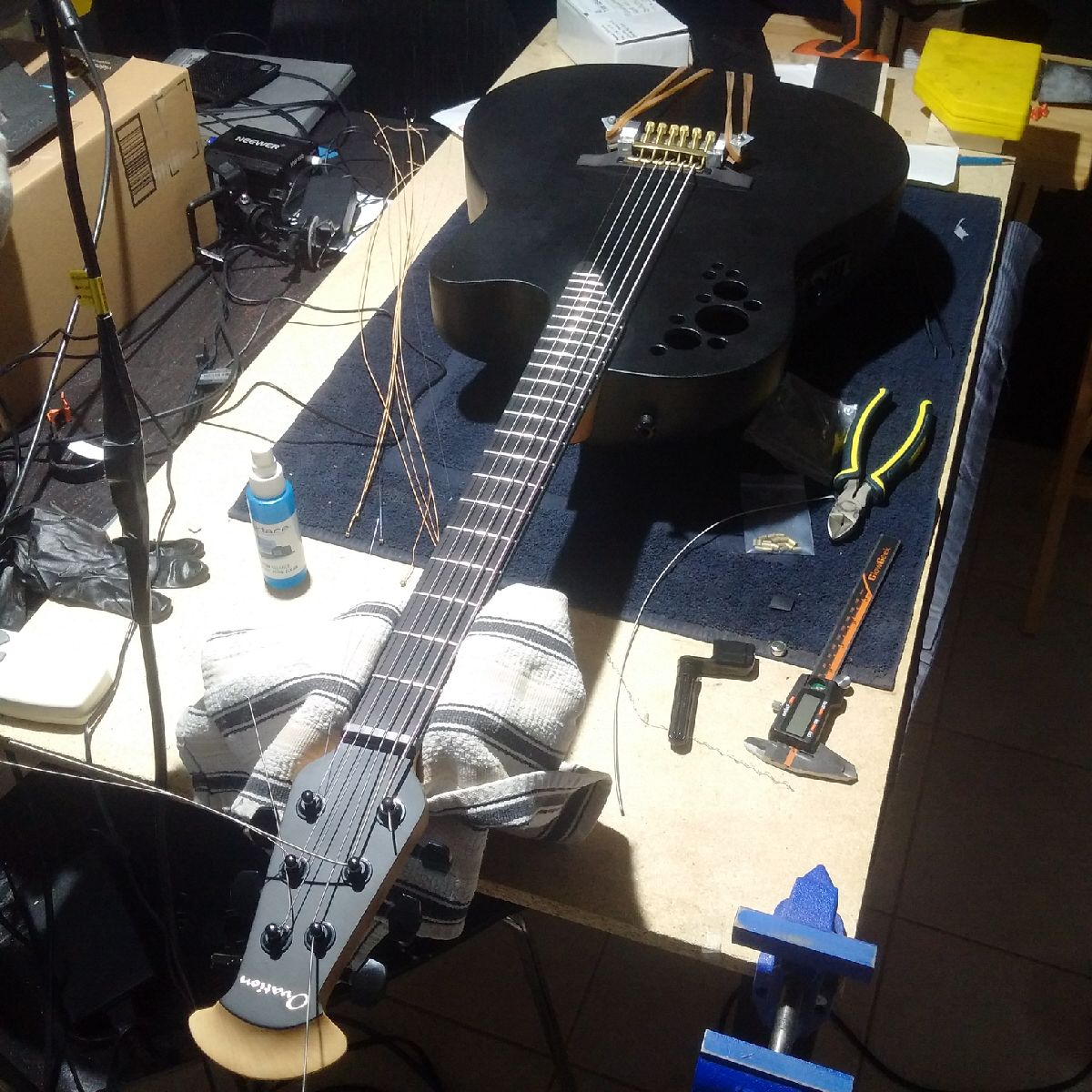
The Intonator was empirically adjusted to find appropriate break points on the saddle and was test-played a lot. Once the points were settled on, a huge inconsistency in the open position of the 90-gauge (low A#) string made Leigh determine that something revolutionary was needed – the Detsom Shelf, a 0.2″ long extension of the nut on only the lowest string.
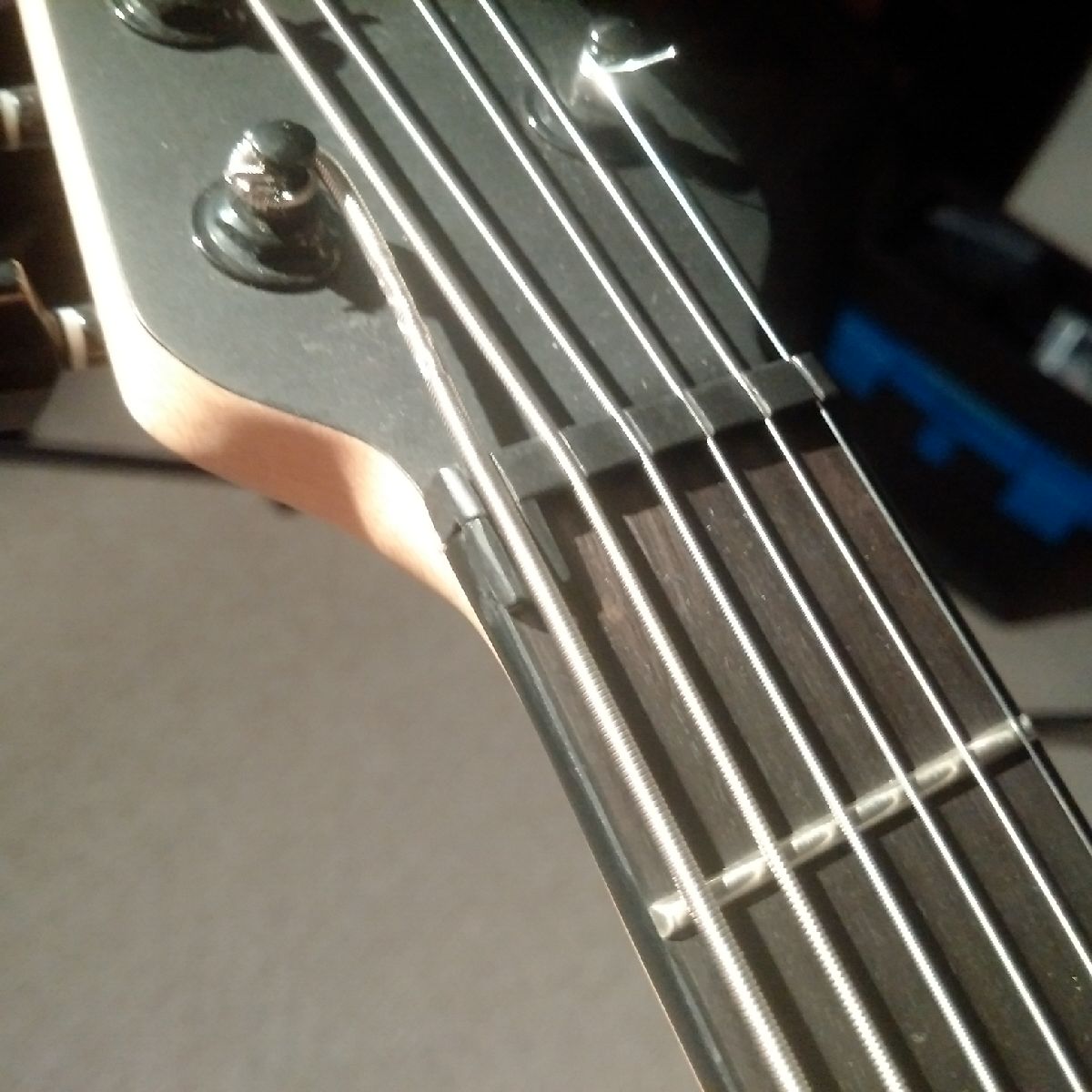
Next, it was time to fabricate a shelf saddle in a similar fashion to the flat saddles developed earlier, but this time it would be a permanent fixture. It was also made from a GraphTech piece, for nut and saddle blanks.
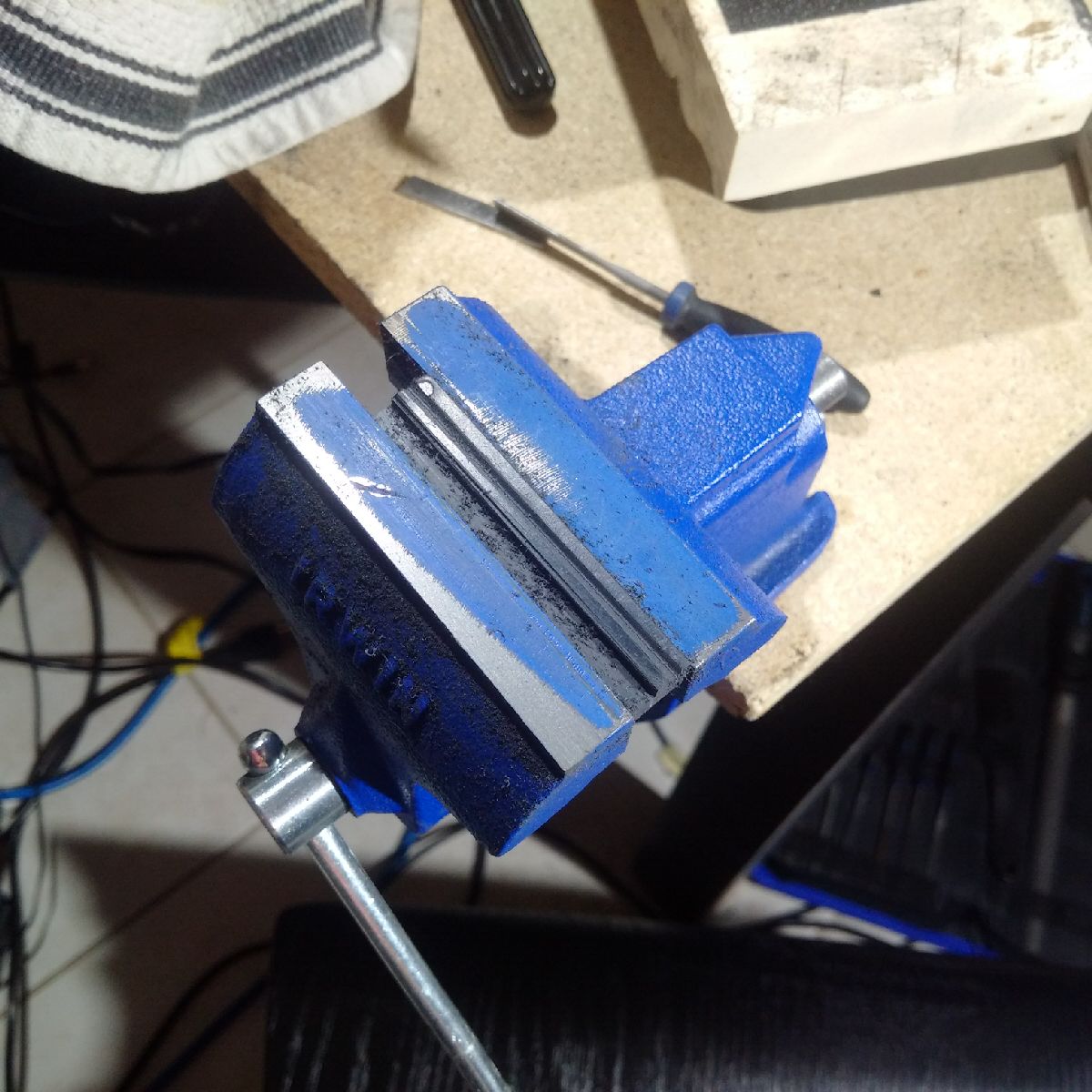
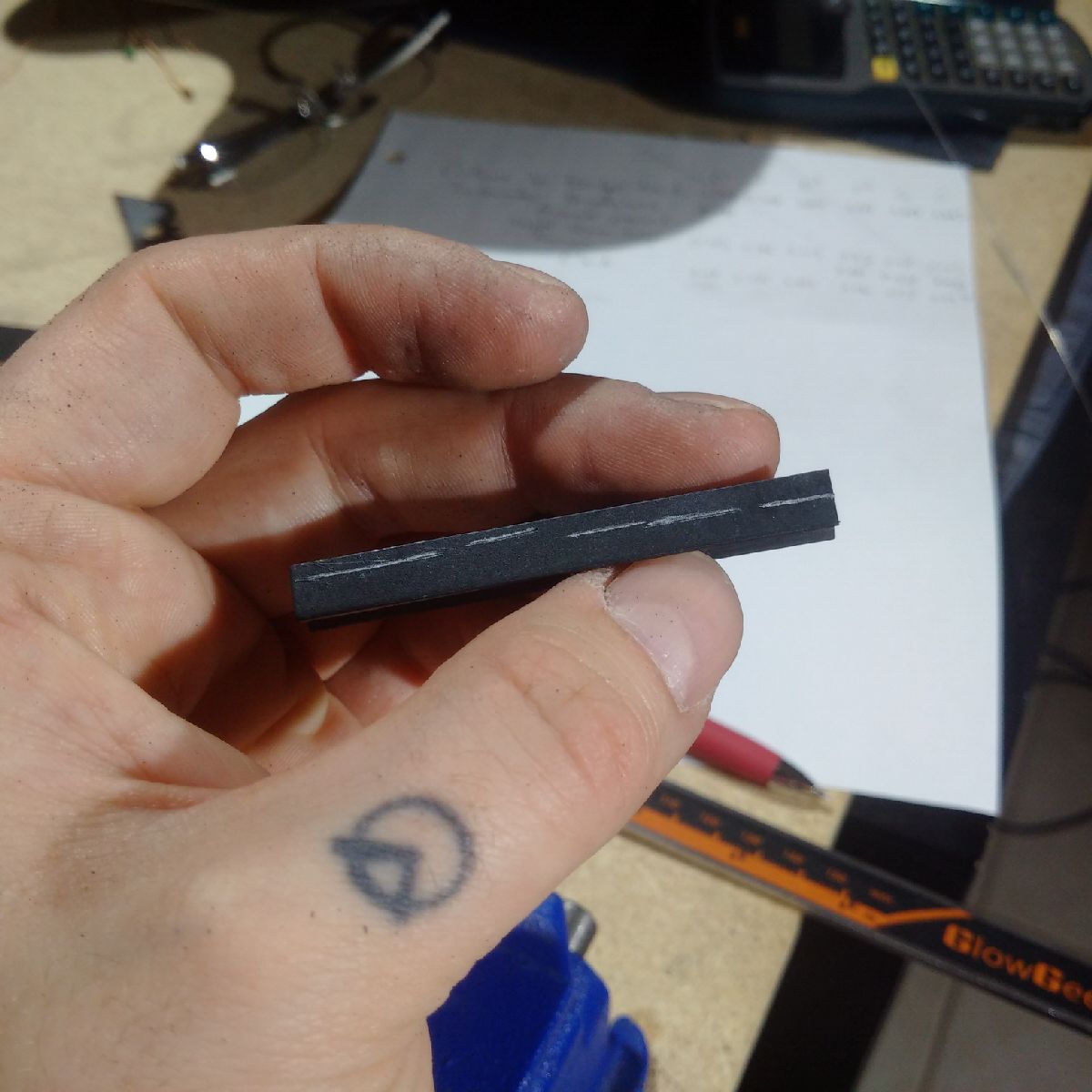
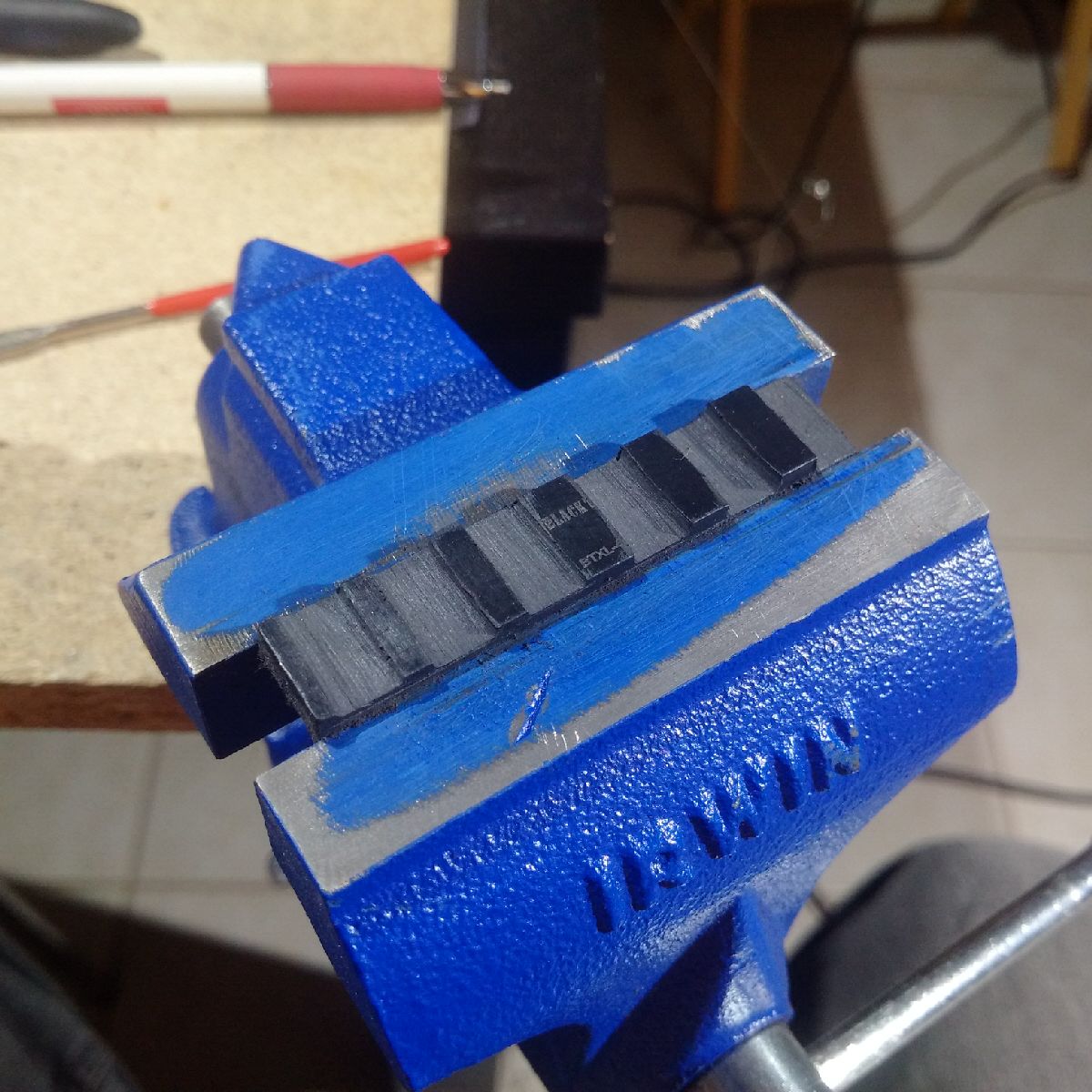
The saddle was fabricated with appropriate break points and fitted into the slot. A pretty good shelf saddle, you might say.
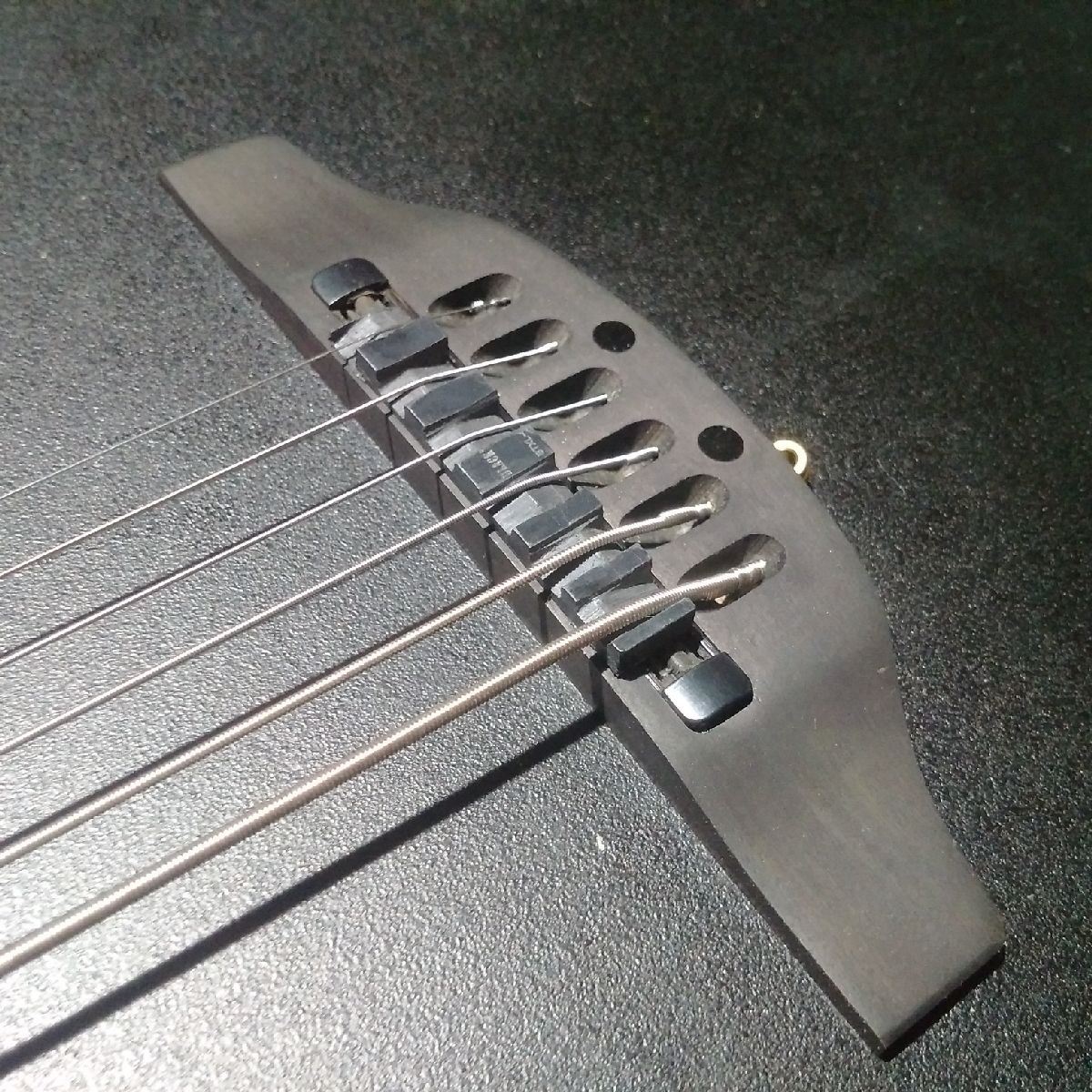
And Leigh were done and ready to play, and play often.
The good thing about having a baritone guitar already in Drop A# was the ability to do a direct comparison. The baritone obviously has a huge advantage already in terms of intonation, but the difference can be heard.
(Note, the exact position of the saddle break points and how they were determined wasn’t revealed just in case that would be a violation of the Buzz Feiten patent – Leigh is still checking with Buzz Feiten to ensure providing that information here is acceptable).
Baritone guitar in Drop A#, standard intonation and no setup:
Detsom method downtuned guitar: